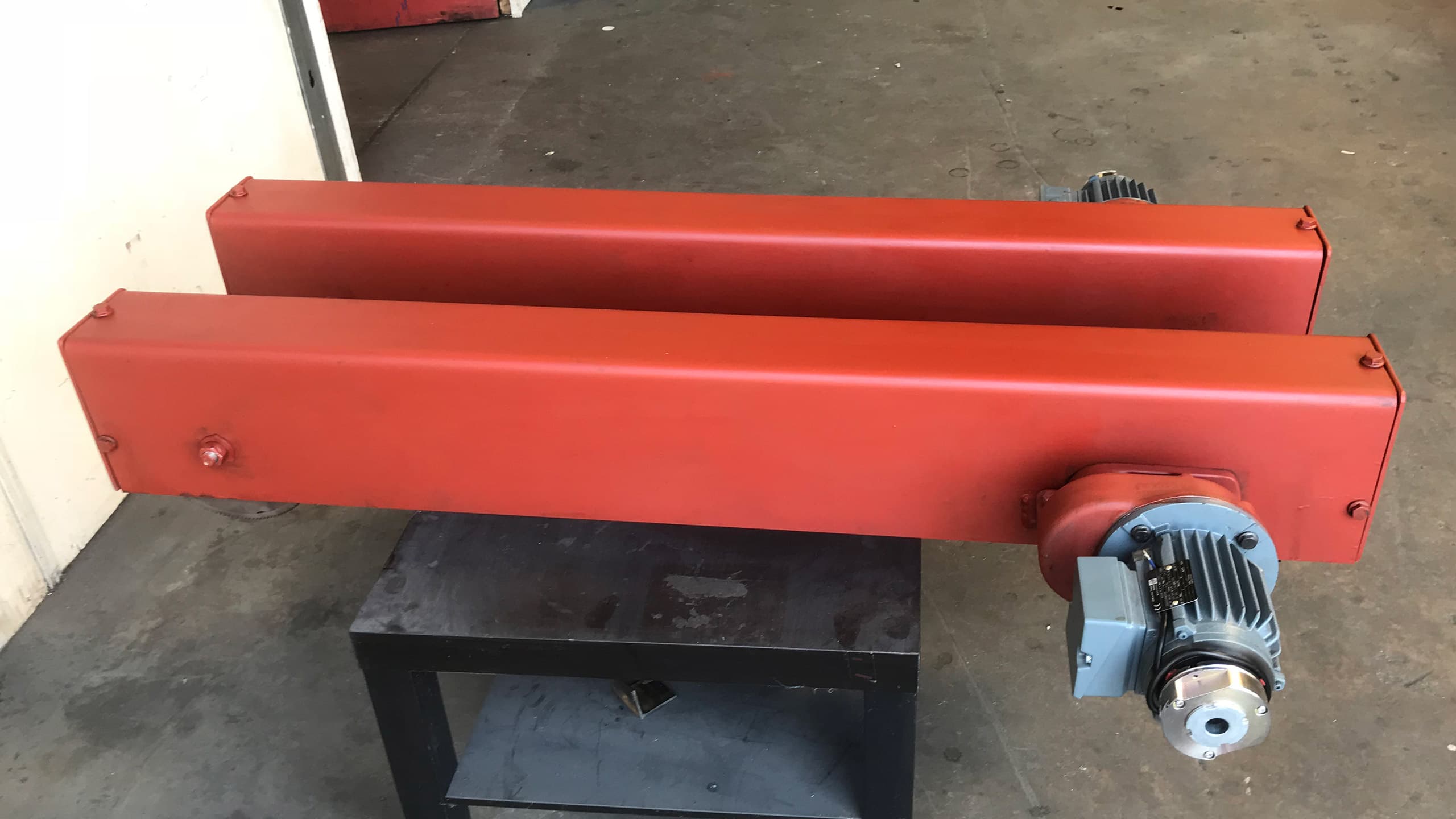
TRAVEL DRIVE UNITS: BUILT-IN RELIABILITY
For years we at Doity Engineering Ltd have been at the forefront of engineering Innovation turning bright ideas into a rewarding reality. In 1956 we pioneered the first individual driven Crane End Carriage that revolutionised the industry sweeping away the accepted method of line drive shafts. This new concept also offered solutions to a host of drive problems in a diverse range of applications and industries.
Our policy of offering quality equipment with in-built reliability has established our reputation as second to none. An example of this was our exploitation of spheroidal graphite iron, 20 years ahead of any other company, for track wheels and gears which doubles the life of components.
Our stocking levels are substantial to allow us to meet 24-hour delivery requests on standard units and our wide range of motor speeds and powers coupled with many ratios of gearboxes gives a large selection of travel speeds from 4.7 Metres per minute to 90 Metres per minute. The introduction of secondary gearboxes allows us to achieve ultra-slow speeds of under 0.5 Metres per minute.
We can supply full sets of Spare Parts for all our Travel Drive units including the many units we have out in use around the world. Our technical engineers are available to discuss unusual projects and advise best solutions.
TECHNICAL SPECIFICATION
All our Travel Drive units are based on Production Engineering techniques and therefore are available in standard format. However, we can modify that format or fabricate units to suit specific requirements, even producing special features such as bronze anti-spark wheels, explosions proof motors and special speeds, be they ultra slow or fast, or flangeless wheels with tyres.
All units are built to our internal quality systems and tested before despatch. Full documentation can be supplied when required.
DRIVE UNIT EXAMPLES
TRANSFER CONVEYOR
This example is typical of many trolley transfer applications where the payload could be carried on rollers or a special cradle, or if the product is granular or liquid, the carrier would be a vessel of appropriate design.
ROTARY OVEN
By slight angling of the drives or removal of the inner flanges of the wheels the units can be successfully employed on curved rails as in the case in this application.
MOBILE BUILDINGS
In exposed conditions such as shipyards, production often drops during severe weather conditions. By supporting interlinked building sections on drive units manufacturing can continue undercover. The building can be opened to allow access or removal of the work-piece and re-sealed to resume production.
ROTARY MILL
In this application, where components need de-burring the rotary mill is supported on two pairs of wheels which provide all the drive necessary to rotate the drum.
SCISSOR LIFT
Basically this is another example of a transfer trolley system that allows the payload to be moved both horizontally and vertically.
OSCILLATING BLENDER
A variety of blender applications have utilised drives where mixing and weighing are part of the process. Control can be accomplished via limit switch stations and the process can be completely automated.